Erodierprozess abgelöst durch Spanprozess
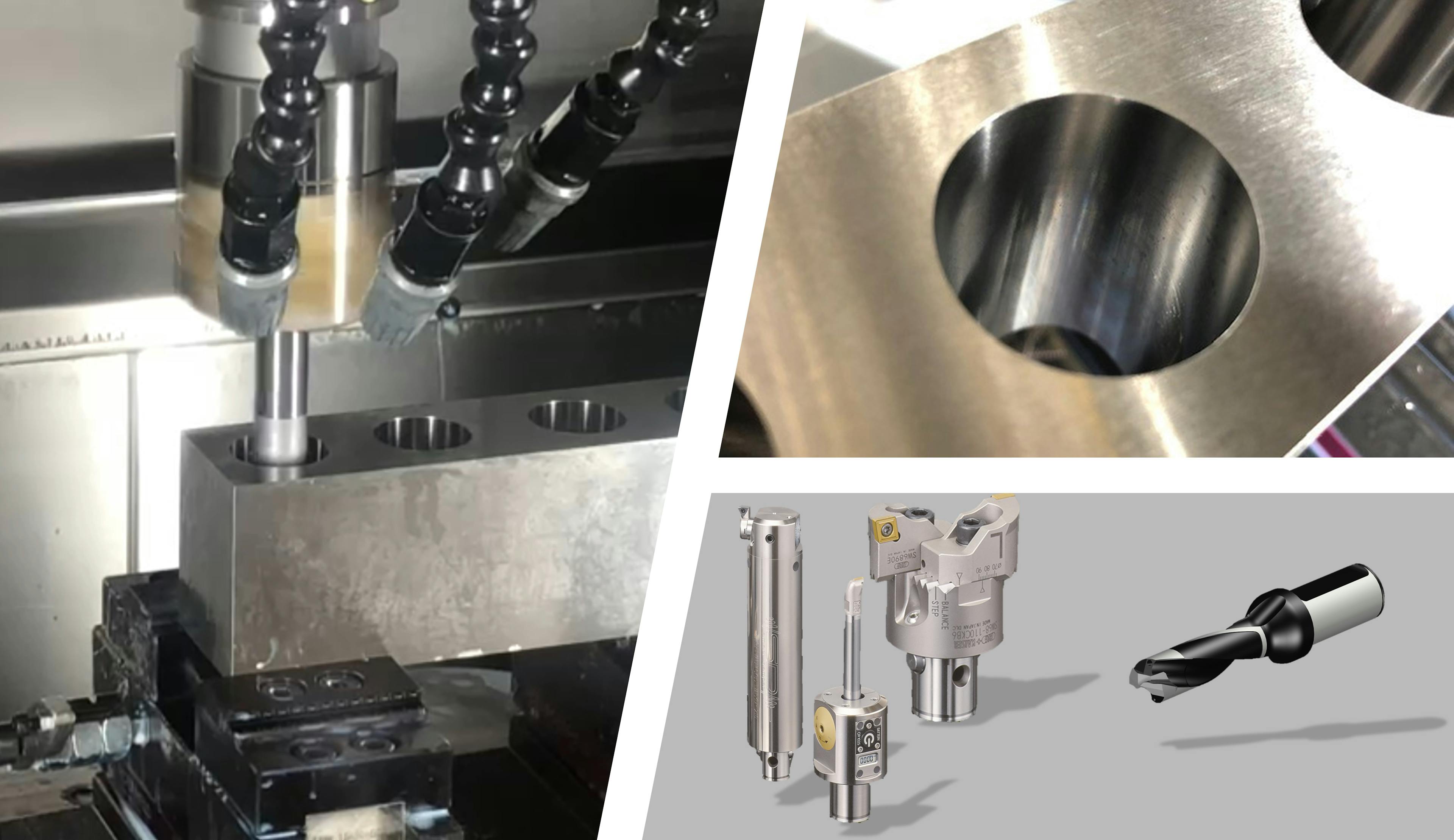
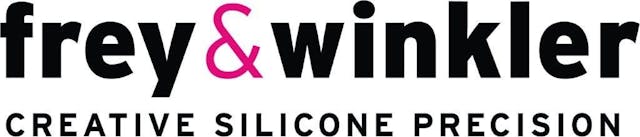
Unser Kunde Frey und Winkler GmbH wollte ein optimiertes Bearbeitungsverfahren für seine Spritzguss-Fertigung. Ein Spritzwerkzeug besteht generell aus mehreren Formplatten, in denen einige Säulenbohrungen mit verschiedenen Durchmessern eingebracht werden müssen.
Vor Ort stellte sich die Ist-Situation als folgende dar: Es wurde ein Rohteil mit Vorbohrungen, verbunden mit Mehrkosten, bestellt. Danach fand die Materialhärtung und zum Schluss die Drahterosion statt. Dabei dauerte allein das Erodieren auf den gewünschten Durchmesser drei Stunden pro Bohrung. Somit war der bisherige Ablauf geprägt von langen Durchlaufzeiten und hohen Maschinenauslastungen.
Jetzt wird das Rohteil ohne Bohrungen und damit günstiger bestellt. Die Kernlochbohrungen erfolgen mit einem Sandvik Wechselkopfbohrer, anschließend wird das Material gehärtet und ausgespindelt. Für die Auswahl und das Einfahren des Ausspindelwerkzeugs unterstützte uns ein Anwendungstechniker von BIG Daishowa. Das Ausspindeln dauert jetzt 8 Minuten in drei Durchgängen – Pro Bohrung werden 20 Sekunden benötigt.
Das Ergebnis in puncto Oberflächengüte, Form- und Lagetoleranzen führte am Ende zur vollen Kundenzufriedenheit! Bei 100 Bohrungen ergibt sich für ihn eine Gesamtersparnis von rund 15.000€ pro Jahr!
Sie finden den Sandvik CORODRILL® 870 Wechselkopfbohrer unter: 870-2500-25L32-3
Falls Sie ebenso eine Optimierung in Ihrer Fertigung wünschen, dann zögern Sie bitte nicht, uns zu kontaktieren!